How to Extend the Cycle Life of Your Valve
What can you do to maximize the life of your valves? Valve cycle life is the valve's expected life under ideal conditions, but few applications are ideal. An understanding of the factors that affect valve life is important for selecting the proper valve and materials.
A valve's cycle life is a reference point for how many cycles the valve could be expected to function in an ideal or standard application. This could also be referred to as the mean time to failure. One cycle for a valve is defined as the valve going from the unactuated state to the actuated state and returning to the unactuated state. In most applications, the cycle life of the valve is measured from when the valve was installed to the time that the valve—in some way, shape, or form—failed. The definition of failure can vary from application to application. Certain applications may see minor leakage and determine the valve has failed, while other applications may not consider a valve failed until the valve ceases to actuate. The cycle life of a valve is for reference only and is not a guarantee of the expected performance from a component.
Pressure
Temperature
Cleanliness
Cycle Rate
Lubrication
Materials
Construction
What Factors Affect the Cycle Life of a Valve?
There are many factors which influence the life of a valve, including: pressure, temperature, cleanliness of the media, cycle rate, lubrication, seal material, and valve construction. Depending on the application, there may also be other additional factors.
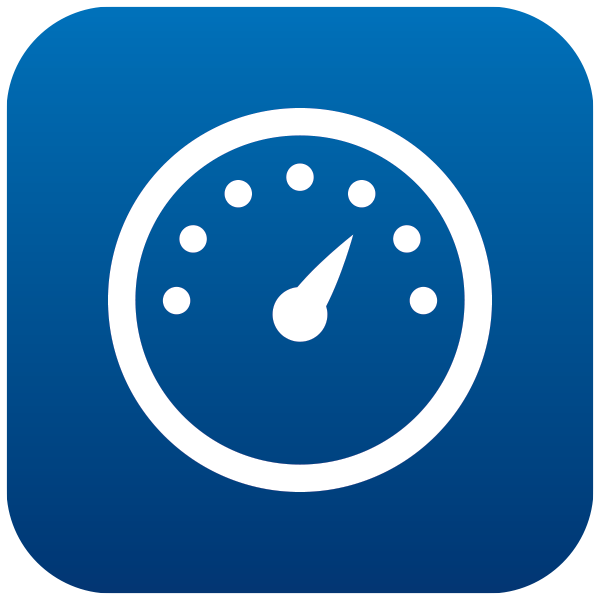
Pressure
Excessive system pressure or spikes in pressure can increase the wear on seals and may even damage them. In extreme cases, exceeding rated pressures on valves can lead to catastrophic failure such as cracking parts that compose the valve, or even breaking the valve and launching components, which can be dangerous.
Compared to spool valves, poppet valves generally have higher pressure ratings due to the fact that on a spool valve, high pressure can push harder on the seals and create extra wear on them. However, exceeding the rated inlet pressure on a poppet valve can damage the poppet seal or lift it off of the seat and create a leak.
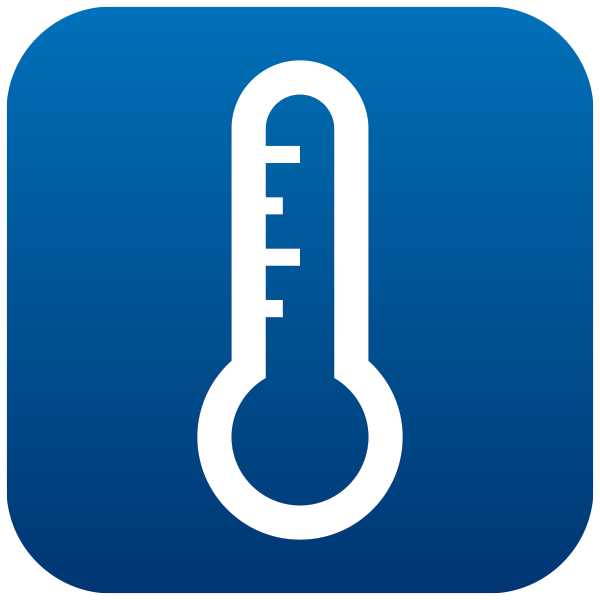
Temperature
Temperature extremes can have a major impact on the life of a valve. Below 32°F, any moisture in the pneumatic systems can freeze into shards of ice. These ice shards can cut and damage seals in the valve. Moisture can also freeze on valve components, preventing valves from actuating. This is why some manufacturers will only rate valves down to 32°F. High temperatures can also break down seal material and cause failures. For example, a stainless steel valve with nitrile seals will see decreased cycle life if used outside the temperature specification for nitrile. For reference, this seal material property chart outlines temperature ratings for a variety of different seal materials. However, temperature extremes are not limited to only affecting the seals of a valve. For example, on many electronic valves, extreme heat can melt the coil encapsulation material and cause the coil to fail.
Compared to spool valves, poppet valves have relatively good resistance to extreme temperatures. With minimal friction, actuation of most poppet valves does not generate additional heat and is not dependent on lubrication. By contrast, spool valve life is not only dependent on the seal material in the valve, but also its lubrication. High temperature applications can turn lubrication into a liquid that is flushed right out of the valve, while low temperature applications can freeze lubrication, preventing the spool from shifting.
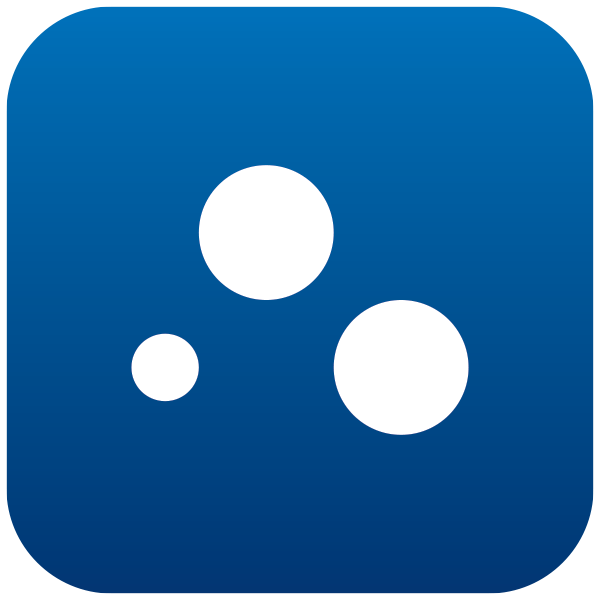
Cleanliness
Contaminated media can quickly destroy a valve. Contamination is anything in the media that is not intended to be there, which can include—but is not limited to—water, metal shavings, or dust. It only takes one tiny piece of debris to damage the seals in a valve. A metal shaving can cut and destroy seals, and dust can build up causing leaks and wear to seals. Manufacturers of valves publish a micron rating for filters that should be used with their valves. Using the appropriate filtration system can help to maintain clean media and extend the life of your valve.
Compared to spool valves, poppet valves have decent resistance to debris in the media. Debris in poppet valves can sometimes get stuck on the poppet seal and cause a leak, but it can also sometimes be flushed off the poppet. If the debris did not cut the poppet seal, there would be little to no noticeable damage done. Spool valves, however, can easily be damaged by debris in the media. One piece of debris on a seal that slides across the housing is all that it takes to destroy a seal in a spool valve.
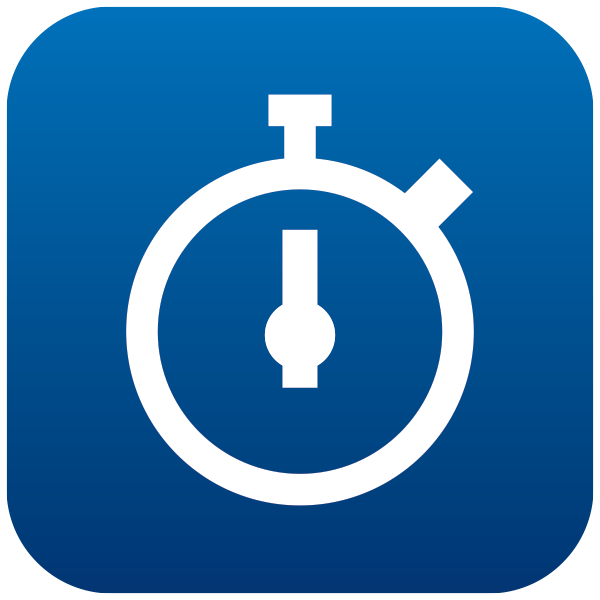
Cycle Rate
The cycle rate of a valve is the frequency that it is actuated. Some applications cycle a valve once a day, while others cycle a valve tens of thousands of times a day. High cycle rates can generate heat from friction which can lead to premature failure.
Compared to spool valves, poppet valves perform very well in high cycle rate applications. Since the poppet seal simply lifts on and off of the seat, this results in little wear and heat generation. This allows poppet valves to achieve high cycle counts with minimal degradation to the valve's life. However, high cycle rates can adversely affect the life of spool valves as the reciprocal action of sliding seals can generate friction, heat, and premature failure.
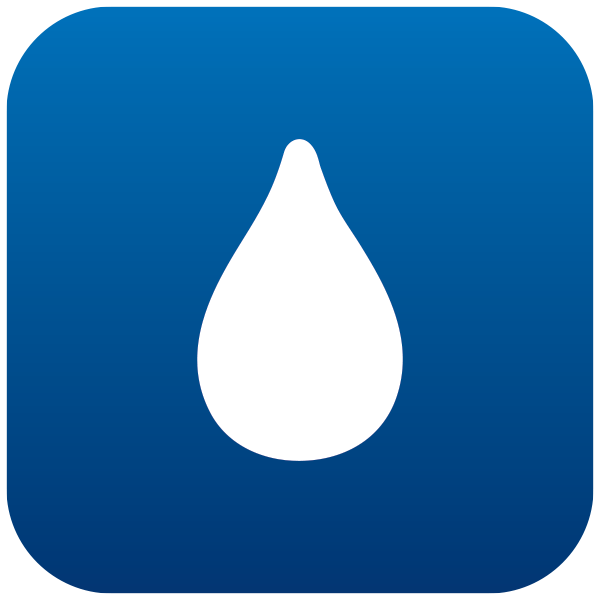
Lubrication
Depending on the valve's construction, some valves will require lubrication for the maximum cycle life. Lubrication can reduce wear on seals and help to reduce heat generated from cycling. It is important that any lubrication used in a valve is compatible with the materials that compose the valve and the media that will go through the valve, and that it is appropriate for the application. For example, certain applications—such as food and beverage, or medical applications—may be limited on the lubricants that are allowed to be used. Other analytical applications may not be able to use any lubrication due to outgassing. Therefore, lubrication restrictions of the application may limit a valve's cycle life.
As mentioned earlier, due to their frictionless cycle, poppet valves are not dependent on lubrication. By contrast, for a spool valve to achieve maximum cycle life, proper lubrication is important for reducing friction and wear on seals.
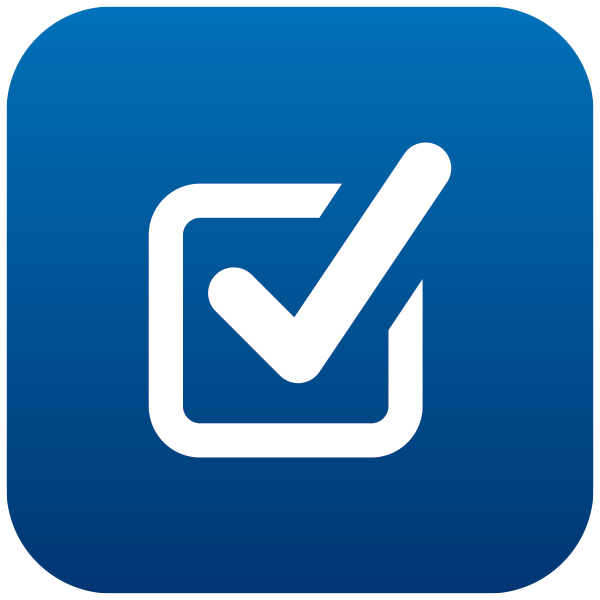
Materials
Valve seals are crucial for the prevention of leaks—both internally and externally. To choose the most appropriate seal material, it is important to consider not only the media the valve will handle and the application for the valve, but also the shelf life of the seal material. For example, a valve that is controlling the flow of an aggressive media will require seals that are compatible with that media. When selecting seal material, references such as Clippard's Material Properties Chart provide a useful comparison of temperature ratings, shelf life, and other factors.
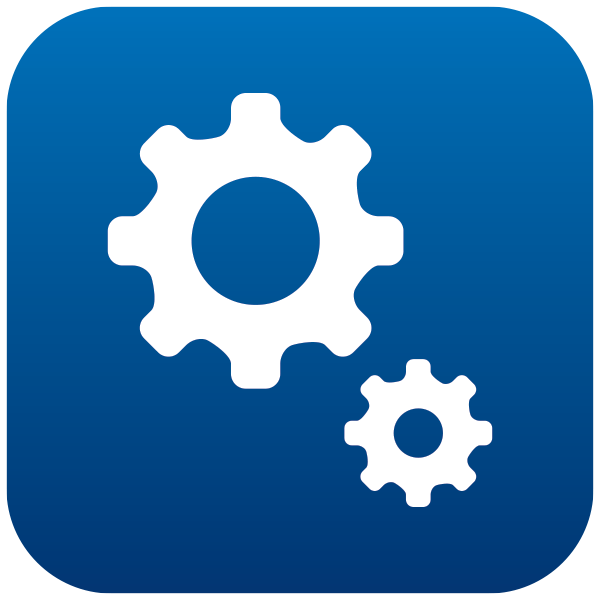
Construction
Valve construction can include the valve style, the actuator type (e.g., electronic, manual, air pilot), and the materials that compose the valve. There are also other types of less common valve constructions which, in addition to being affected by all the aforementioned factors, may also have other life restrictors. For example, stepper actuated valves, pinch valves, and piezo actuated valves are less common and could have other factors that affect life and performance.
When Does Cycle Life Matter?
Valve manufacturers design and build valves to exceed the standard requirements that most customers require for most applications. Yet, some applications demand billion of cycles while other may only need a few cycles. For example, a valve that delivers oxygen with every breath would need to work every time and may cycle millions of times in a year; while a valve that supplies compressed air to an assembly area may only be actuated once or twice a day. For an industrial valve that is cycled once, twice, or even dozens of times a day, cycle life may matter very little. However, for a valve that is delivering oxygen to a patient and must function perfectly every time, cycle life becomes very important. In this case, there is a significant benefit to having a valve that is proven to last well beyond the required life as it is likely to provide higher reliability.
How Can Valves Be Modified to Improve Cycle Life?
There are many factors that contribute to the cycle life of a valve. Because of this, adjustments can often be made to standard valves to better adapt them to meet the needs of specific applications. In many cases, this is where working together with a knowledgeable manufacturer will deliver a superior performing product.
For example, in one particular application, handling blood samples in a blood analysis machine required a minimum of 4 million cycles. However, standard valves used in the application were only able achieve 1 million cycles. Clippard's engineering team researched the issues that were limiting the cycle life of the valves and determined that it could be extended by changing certain materials within the valve. This change was easily implemented, prototyped, and tested, resulting in a new, custom valve that not only met but exceeded the 4 million cycle target.
In a different application, mobile equipment was failing prematurely due to usage in an extreme environment. Mobile applications can be highly demanding—certain types of equipment may be in the desert one month, and the arctic another month. These extreme temperature variations can be tough to conquer, and when the valve is controlling vital machine functions, it must work properly every time. In this case, Clippard's engineers started with the 1 billion cycle DV series electronic valve. With modifications to the coil, seals, and poppet seat they had a valve that was soon proven to handle the wide range of temperature fluctuations this application required.
The cycle life of a valve is the valve's expected life under ideal conditions. Not all applications are ideal, so understanding the factors in the application that affect the life of the valve is important for selecting the proper valve and the proper materials. Standard valves often meet or exceed the requirements, but sometimes modifications are necessary to better valve adapt the valve for the application. In many cases, simple adjustments can be made resulting in a product that delivers superior performance. If you need help extending the cycle life of your valve, contact Clippard or your nearest Clippard distributor for assistance.
Was this content useful? Provide Feedback
By Mike Kettering • Technical Sales Specialist • Clippard
Related Content
- Special Materials for Demanding Applications
- Material Properties Chart
- Poppet Valves vs. Spool Valves