Critical Aspects of a Valve's Internal Design
Out of sight often means out of mind, but when valves are concerned, that which is out of sight should be top of mind—at least during valve selection. This paper will discuss key internal design characteristics a valve should have in order to meet high efficiency, critical control demands common in pharmaceutical, medical, or analytical applications. These design features include the valve's flow path, dead space, flushability, and internal volume.
Flow Path
For fluids susceptible to hemolysis or homolytic fission—in which the cells or compounds within the fluid break down—minimizing turbulence as much as possible is a high priority in order to prevent the loosening of chemical bonds. Therefore, the smoother a valve's flow path, the better. This lowers cost and waste where expensive reagents and solvents are required, as well as in applications where the primary medium is blood.
Dead Space
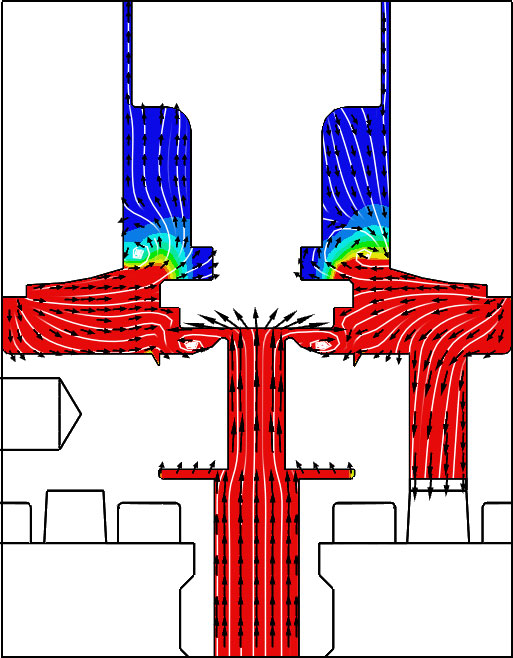
Figure 1: Example of dead space zone
Dead space is a zone within the valve where flow stagnates and often "whirls in place," such as in corners and tight locations between a valve's components outside of the direct flow path. This can be seen in Figure 1, a cross-section of a valve typically used for air. The blue areas have a velocity of less than 0.2% of the maximum seen in the inlet of the valve, and the white swirls indicate flow paths with the black arrows indicating direction. The blue zones are determined to be dead space due to the comparatively low velocity. Dead space is detrimental to the quality of the medium leaving the valve, as traces of the medium get trapped in these zones and can contaminate new flow going past, introducing old particulates and even hazardous compounds such as mold or decayed particles into the fluid. Minimizing—if not eliminating—dead space is vitally important to ensuring consistent medium quality in sensitive applications, such as in the medical field.
Flushability
In instances where a high level of cleanliness is required, either for safety or analysis purposes, valves are flushed in a further effort to prevent contamination by clearing the "wetted" surfaces. This ties back to dead space, as the valve can only be as clean as it can be flushed. Valves with extensive dead spaces must be flushed multiple times and with different types of solutions to ensure no residue of prior runs remain, which is costly and time consuming.
Internal Volume
Another design aspect that goes hand-in-hand with the preferred flow path characteristics discussed above is internal volume. Minimizing internal volume means reducing the wetted area—the surface area the medium contacts—as well as the total wetted surface area. This has a huge impact on improving efficiency and lowering cost in situations where flushing the valve is required after each use. Typically, when the internal volume is designed to be as small as possible, the dead space is automatically reduced, which makes the valve more flushable and the flow path smoother. This in turn saves time and money in operating the valve for its intended purpose.
An additional condition that should not be overlooked is temperature. Most valves radiate some amount of heat due to motors or coils, therefore, in heat-sensitive scenarios where the fluid needs to be kept beneath a certain temperature, it is often best to limit exposure inside the valve. Low internal volume often reduces the amount of exposure a fluid has to heat, which can in turn lead to money savings on temperature control systems.
Conclusion
When selecting a valve, always consider how the fluid is moving through the valve and how that will influence the application. To be cost efficient, there are some situations when having low internal volume or even smooth fluid flow is not a must, but in critical systems where cleanliness and sample quality is a priority, be sure to look inward. Internal design matters.
By Jess Koeniguer • Design Engineer • Clippard
Related Products |
||||
Eclipse Proportional Isolation Valve ![]() |
NIV Series PTFE Isolation Valve![]() |
NPV Series Electronic Pinch Valve![]() |
NPP Series Pneumatic Pinch Valve![]() |