Comparing Poppet Valves vs. Spool Valves
Two of the most common designs for pneumatic control valves are the poppet and the spool. A poppet valve consists of an orifice that is opened and closed by raising and lowering a sealing surface onto the orifice. It usually has an internal spring that holds the valve in the closed position. When the spring force is overcome, the sealing surface lifts off the orifice and the valve opens. A spool valve consists of a shaft with a series of O-rings inside of a barrel. As the shaft moves back and forth, the O-rings shift position to open and close different flow paths.
What Are the Benefits of Poppet Valves?
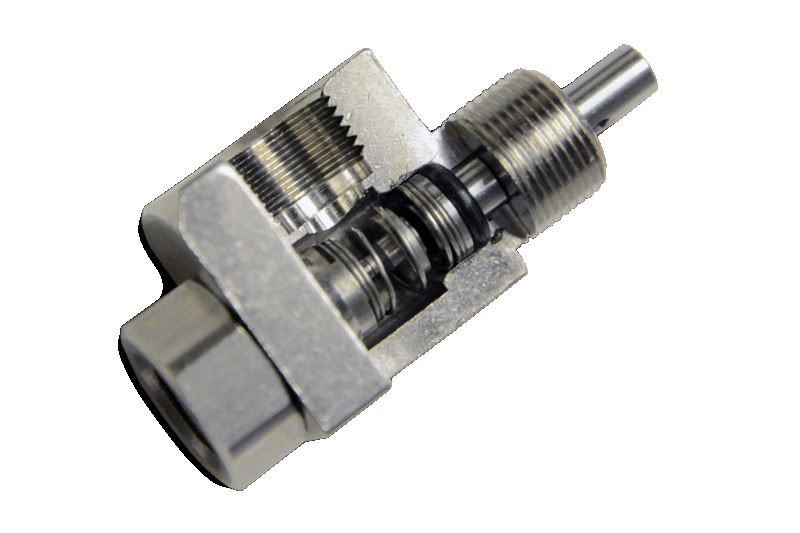
A poppet is a valving element that seals on a valve seat. A return spring and the inlet pressure assist in sealing the valve. Compared to spool valves, poppet valves provide certain advantages and disadvantages which make them better suited for particular applications such as those that require precise control, high flow rates, long life, low leak rates, fast response times, or low cost.
What Are the Benefits of Spool Valves?
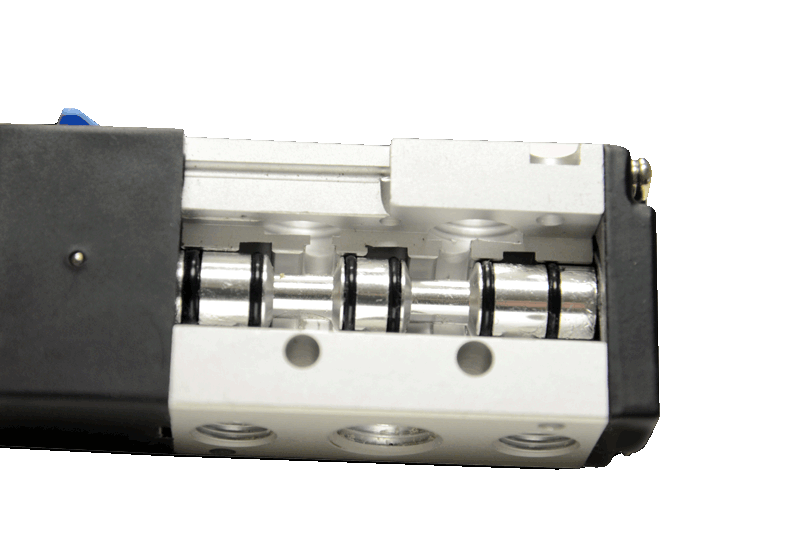
A spool is a cylindrical valve element that opens and closes ports when moved axially within the valve bore. Most spool valves use elastomers to seal between flow paths. Compared to poppet valves, spool valves provide certain advantages and disadvantages which make them better suited for vacuum applications, applications which require holding pressure downstream, selector valve applications, and applications which require consistent response time.
Poppet or Spool—Which Will Work Best for Your Application?
To choose which type of valve—poppet or spool— will best meet your specific needs, consider the factors that are most critical for your application. For example, poppet valves are better suited for applications which require precise control due to the closed crossover (no transitional state from one function to the next). They are also a better choice for applications which require fast response times because they open immediately upon actuation and feature a shorter stroke. However, if your application requires consistent response time or utilizes a vacuum, you should choose a spool valve instead. The chart below serves as a good starting point. Still have questions? Contact Clippard or your local Clippard distributor for assistance.